I definitely want to learn to digitize my own files for embroidery. The prohibitive cost of the software ($1000+) means I probably won’t be doing so any time soon, but Wilcom has a new package called Hatch which I downloaded a 30 day trial of. It’s a full featured digitizer with a (theoretically) easier to use interface. So I’m playing around with it and today I gave the auto-digitizer a spin.
I used this adorable octopus, which Chris designed for hand embroidery on a dress I made a few years ago.
I ran it through the auto-digitizer, setting a blue fill for the body and white fill for the eyeballs. Everything else is satin stitch. I tweaked the fill angles a bit and reordered some of the objects for easier to cut jump stitches, but otherwise left it as-is. Wilcom thinks it will look very nice! There are a little over 14,000 stitches. So it will take about 40 minutes to stitch out, not counting the time it takes me to rethread the machine between colors.
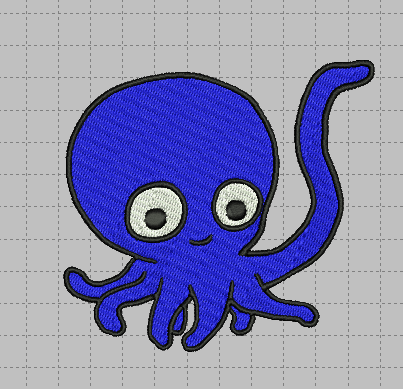
I stitched it out on some “linen look” cotton fabric using medium weight tear away stabilizer.
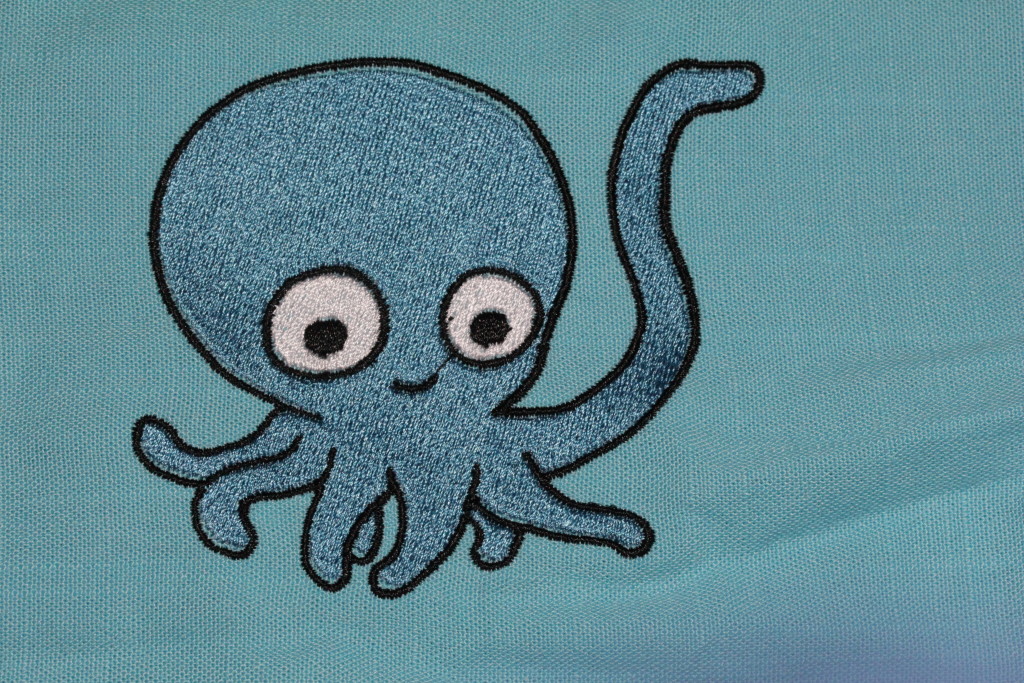
Aside from the jump stitch I couldn’t quite get at with my scissors, there’s noticible pulling at the top of the head and the bottom of the legs.
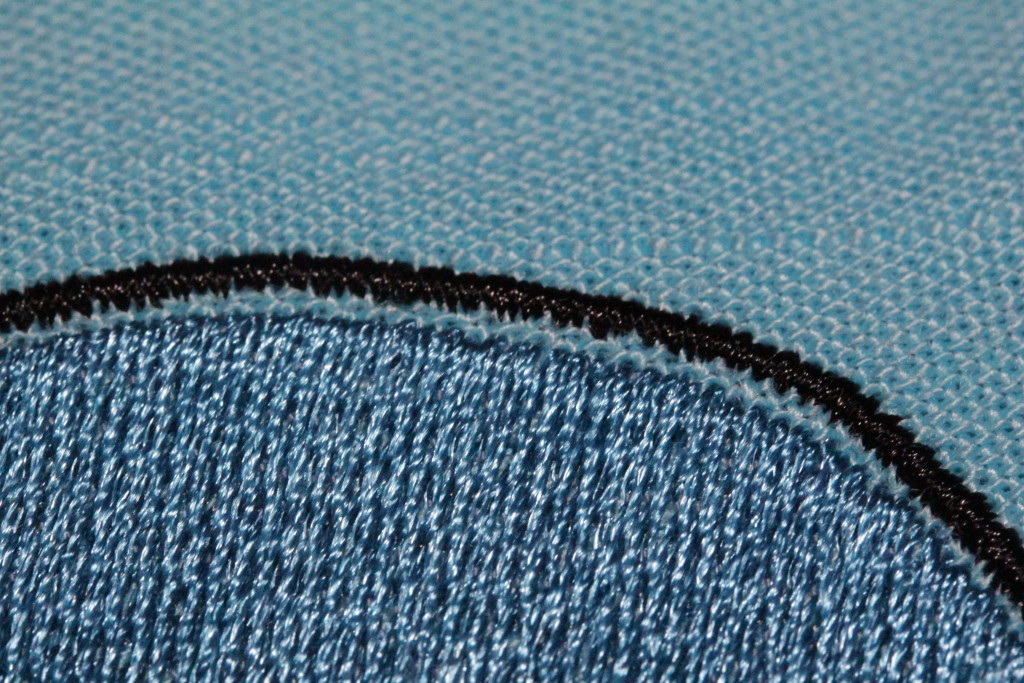
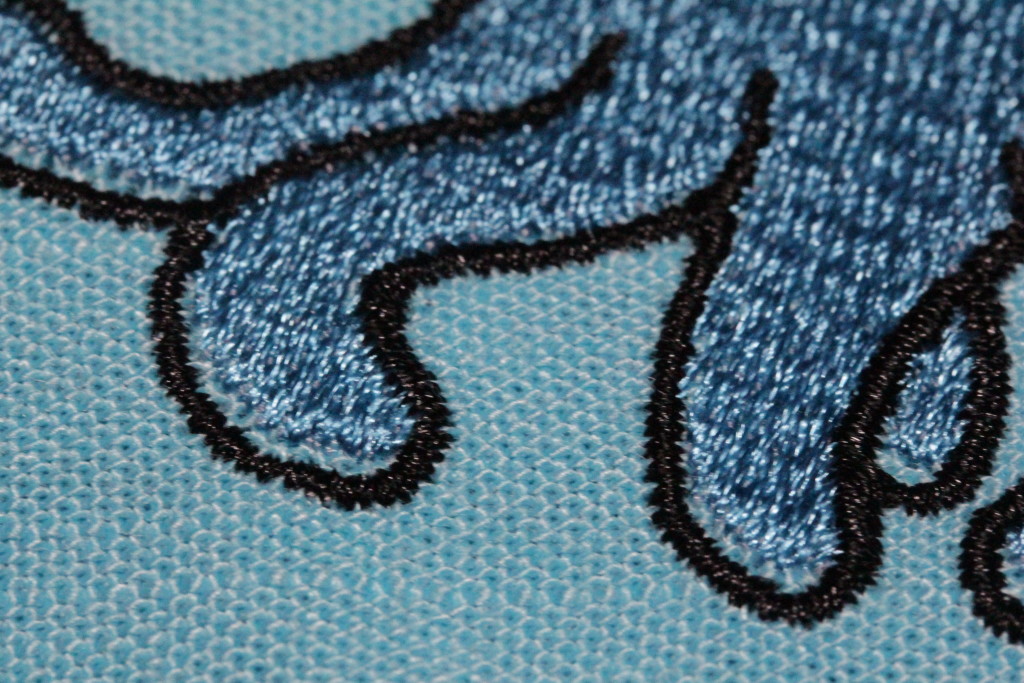
There’s also some around the eyes. This is not entirely unexpected, the stitches tend to pull in, leaving a gap and the vertical edges of the stitches.
I measured the gap at the top with my calipers (0.045 inches) at tried to compensate accordingly by reshaping the objects in Hatch. Then I eyeballed the other gaps and adjusted them too. I stitched out the pattern again, this time with contrasting thread so it’s easier to see how things line up.
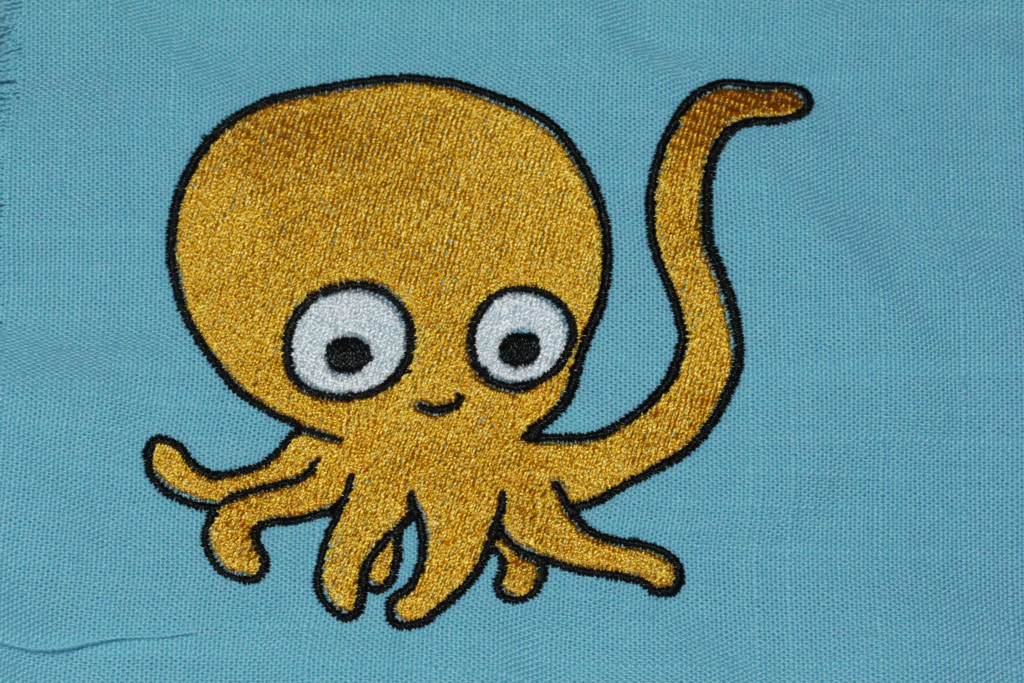
This one came out better, but I was too conservative with my compensation. There are still visible gaps between the outline and the fill.
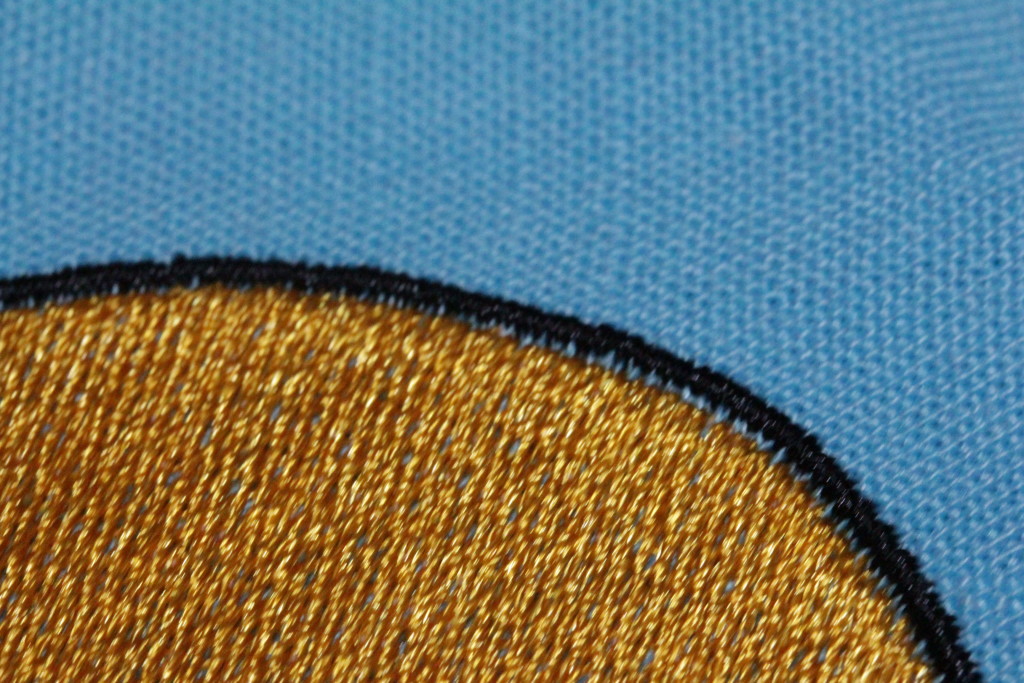
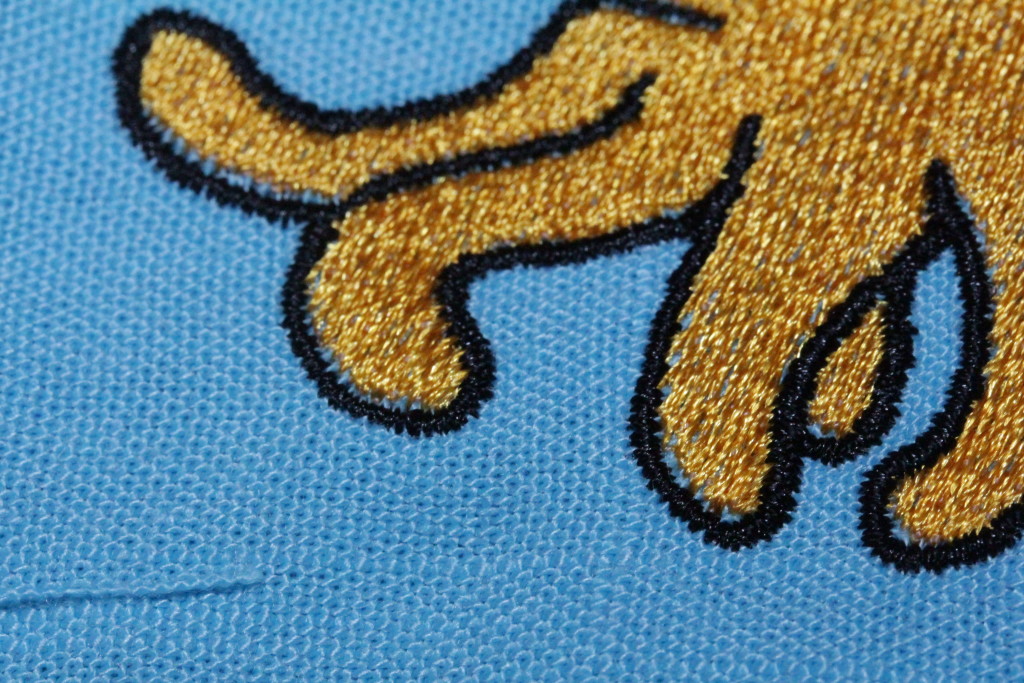
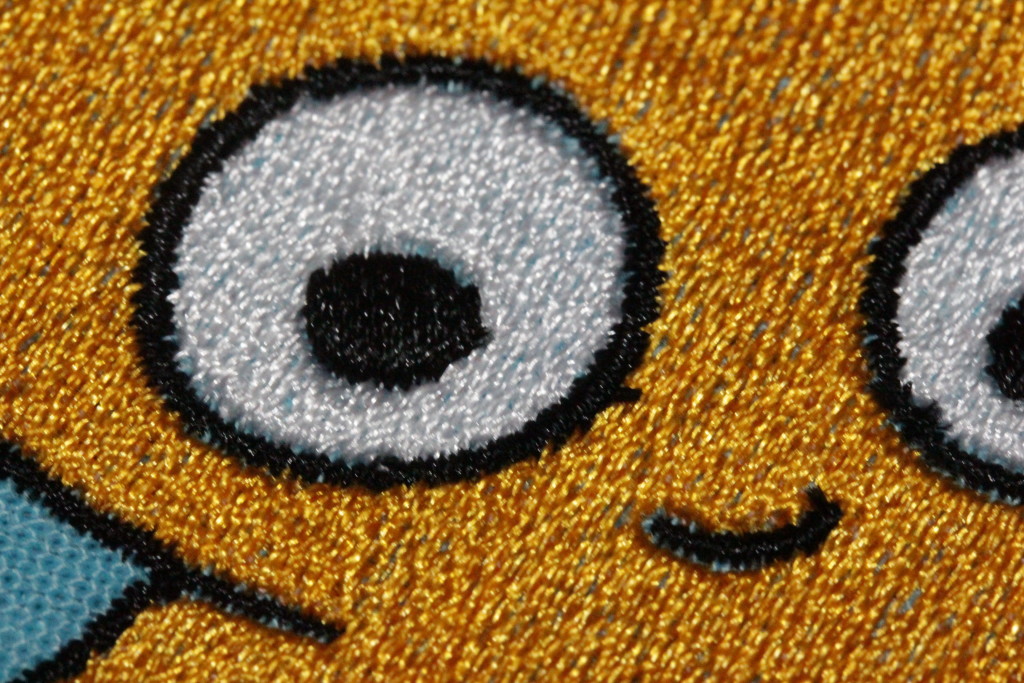
I think with the 3rd round of revisions I’ll get it right, but this has definitely confirmed my skepticism of folks selling purely auto-stitched designs without a sample sew-out to show. A lot of the designs on Etsy have just the computer generated preview, and I suspect many of them have never been tested in the real world. I’m going to play with Hatch a little more to get a feel for manual digitizing, but for complicated or important designs I’m going to continue sending them out to professional human digitizers.